Tips for overcoming supply chain bottleneck
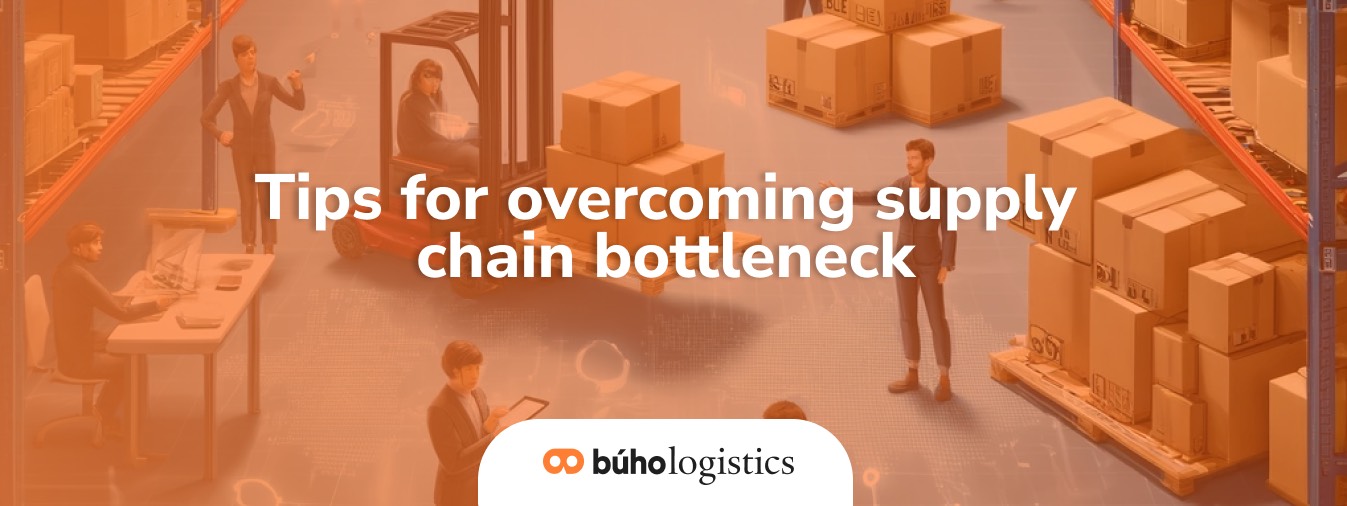
Contenidos
At the beginning of the year, we shared the most common logistics mistakes during the holiday season so you can avoid them and be prepared anytime. However, the holiday season is not the only concern businesses must consider. Supply chain bottlenecks are among the most pressing challenges businesses face today.
These disruptions can occur at any point in the supply chain, whether due to supplier delays, transportation inefficiencies, or unexpected global events. Left unaddressed, bottlenecks can slow production, delay customer deliveries, and significantly impact profitability. Finding ways to navigate these hurdles is essential for businesses aiming to stay competitive.
Overcoming supply chain bottlenecks requires a proactive approach that combines strategic planning, strong supplier relationships, and agile operational practices. By identifying the root causes of bottlenecks and implementing targeted solutions, businesses can improve efficiency and reduce disruptions.
In this article, we will explore actionable tips for overcoming supply chain bottlenecks and building a more resilient operation. From optimizing inventory management to diversifying supplier networks, these strategies can help your business adapt to changing circumstances and ensure smoother operations, even in the face of uncertainty. Whether you’re looking to address current challenges or future-proof your supply chain, these insights will serve as a valuable resource.
What are supply chain bottlenecks?
Supply chain bottlenecks are points of congestion or delays within the supply chain that disrupt the smooth flow of goods, services, or information. These bottlenecks can occur at any stage of the supply chain, from procurement and production to transportation and final delivery, and they often result in slower operations, missed deadlines, increased costs, and customer dissatisfaction.
Bottlenecks typically arise when the demand for resources, labor, or infrastructure exceeds the available capacity. For example, a factory might struggle to meet production targets due to limited raw materials, or a transportation network might face delays because of port congestion.
External factors such as natural disasters, geopolitical events, or supply-demand imbalances can also exacerbate bottlenecks, making them more difficult to manage. In essence, supply chain bottlenecks are the weakest links in the chain that hinder overall efficiency.
3 common causes of bottlenecks
Supply chain bottlenecks can emerge from a variety of sources, often stemming from inefficiencies, unforeseen disruptions, or limited resources. Understanding the root causes of these bottlenecks is the first step in addressing them effectively. Below are some of the most common contributors to supply chain congestion and delays, explained in detail.
1.- Demand-supply imbalances
One of the primary causes of bottlenecks is a mismatch between demand and supply. Unexpected spikes in customer demand, seasonal trends, or inaccurate demand forecasting can overwhelm the supply chain.
On the other hand, shortages in raw materials or production delays can leave businesses unable to meet even predictable demand levels. These imbalances disrupt the flow of goods, leading to delayed orders and dissatisfied customers.
2.- Limited supplier capacity
Suppliers with inadequate capacity can create significant bottlenecks, especially when they are unable to meet production schedules due to resource limitations, labor shortages, or outdated infrastructure.
Relying on a single supplier amplifies this risk, as any disruption on their end—such as a factory shutdown or raw material delay—can halt your operations entirely.
3.- Transportation and logistics challenges
Delays in transportation and logistical inefficiencies are common culprits behind supply chain bottlenecks. Issues like port congestion, insufficient shipping capacity, or disruptions caused by adverse weather can slow down the movement of goods.
Additionally, labor strikes or geopolitical tensions can compound these challenges, creating widespread delivery delays. That’s why we recommend a fulfillment center Mexico.
Strategies for overcoming bottlenecks
Overcoming supply chain bottlenecks requires a combination of strategic planning, innovative tools, and adaptive processes. Below are key strategies for tackling bottlenecks, detailed under specific actionable approaches.
1.- Optimize Inventory Management
Effective inventory management is crucial for preventing bottlenecks. Businesses should implement demand forecasting tools to ensure stock levels align with expected needs.
Safety stock policies can help cushion against unexpected surges in demand or delays in supply.
Additionally, adopting just-in-time (JIT) inventory practices can reduce excess stock and free up resources, though it requires strong supplier relationships and precise coordination to avoid shortages.
2.- Strengthen supplier relationships
Building strong, collaborative relationships with suppliers is key to reducing bottlenecks. Open communication about production schedules, lead times, and potential challenges helps ensure smoother operations.
Businesses should work closely with suppliers to address capacity constraints, negotiate flexible terms, and develop contingency plans for unexpected disruptions. A partnership approach fosters trust and ensures suppliers prioritize your needs when challenges arise.
3.- Implement real-time tracking and analytics
Real-time tracking technologies, such as IoT sensors and GPS, enable businesses to monitor shipments, inventory, and production processes at every stage. Advanced analytics tools can identify potential bottlenecks by analyzing historical data and flagging anomalies before they escalate. With these insights, businesses can make informed decisions quickly, rerouting shipments or reallocating resources to maintain operational flow.
4.- Diversify your supplier network
Relying on a single supplier increases vulnerability to bottlenecks. Diversifying your supplier base ensures that disruptions at one source do not completely halt your operations.
Companies should identify alternative suppliers in different regions and establish relationships with them as a backup. This approach not only reduces risk but also allows for greater flexibility in response to market changes.
5.- Streamline transportation and logistics
Efficient transportation and logistics are essential for overcoming supply chain bottlenecks. You should work with reliable carriers, optimize shipping routes, and leverage technology to improve scheduling and tracking. Implementing multimodal transportation—using a combination of shipping methods such as air, sea, and land—can also minimize delays. Regularly reviewing and updating logistics strategies helps keep operations agile and responsive to changes.
By adopting these strategies, businesses can address existing bottlenecks and build a supply chain that is both flexible and resilient. If you liked our article, share it on social media and stay pendant on our blog for more information this 2025.