Common logistic mistakes during the holiday season
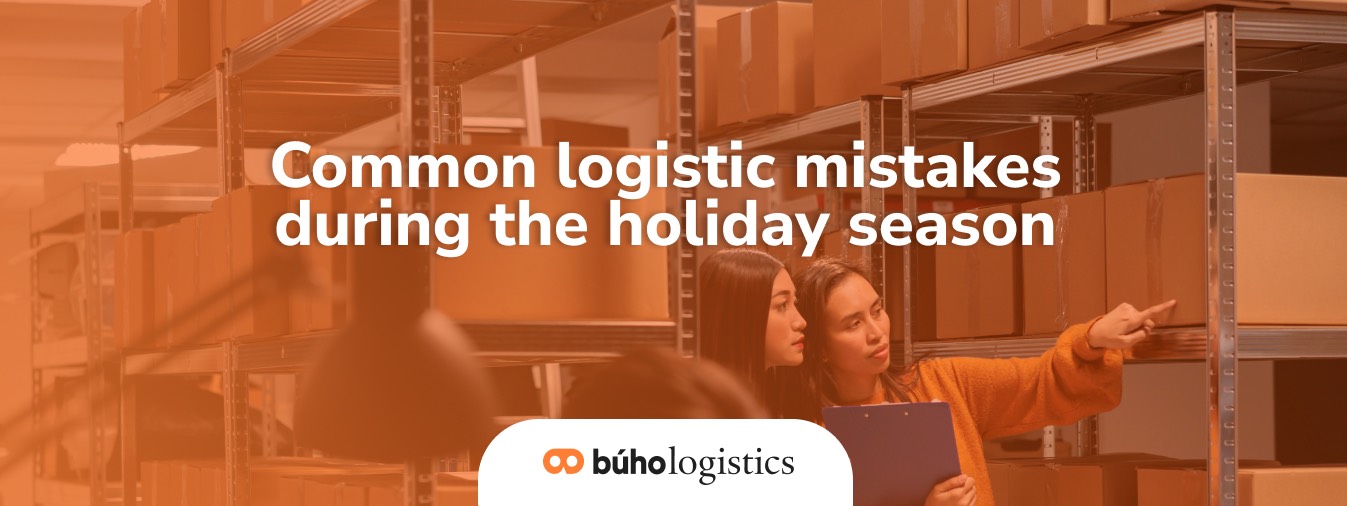
Contenidos
Last week we shared with you some methods to ensure order picking accuracy, however, there are some seasons throughout the year where mistakes can cost not only resources or money but also damage the reputation of your business.
We are referring to the holiday season, even though it is a time of joy and celebration, it also signifies an increase in consumer demand. Here is when businesses seek to boost their sales, strengthen customer relationships, and end the year on a high note.
But, this surge in activity also brings logistical challenges that can disrupt operations if not handled effectively. From inventory shortages to delayed deliveries, even the smallest oversight can lead to dissatisfied customers and lost revenue.
In this article, as a mexican fulfillment center, we’ll explore some of the most common logistic mistakes businesses make during the holiday season and provide practical tips to help you navigate these challenges seamlessly.
The importance of efficient logistics during the holidays
First, we want to delve into why it is important to have efficient logistics. This season, customers expect their orders to arrive quickly and without hassle, especially with the growing popularity of e-commerce and same-day delivery options. A single delay or error can result in not just a lost sale but also damage to your brand's reputation.
Beyond customer satisfaction, effective logistics play a crucial role in maintaining operational stability during this high-pressure season. Without proper planning and execution, businesses risk overburdening their supply chains, leading to inefficiencies and increased costs.
For example, failing to account for shipping delays or not having adequate inventory management strategies can create ripple effects, impacting everything from production schedules to cash flow. Companies that invest in streamlined logistics processes during this period often find themselves better positioned to handle demand fluctuations, minimize disruptions, and capitalize on the season’s opportunities.
By recognizing the importance of logistics and taking proactive measures, businesses can avoid common pitfalls and ensure a seamless experience for their customers. Whether through advanced technology, strategic planning, or strong supplier partnerships, prioritizing logistics during the holidays is a key step toward achieving success in one of the most competitive times of the year.
Common logistic mistakes to avoid
Now, during the holiday season, even minor logistical errors can snowball into major challenges, resulting in unhappy customers, lost revenue, and operational chaos. To help businesses stay ahead, it’s crucial to recognize and address some of the most common mistakes that arise during this critical period. Hereunder you’ll find them.
1.- Underestimating holiday demand
One of the most frequent mistakes businesses make is failing to accurately predict the surge in demand during the holidays. This can lead to stock shortages, leaving customers frustrated and driving them to competitors.
On the flip side, overestimating demand can result in excess inventory, tying up valuable resources and increasing storage costs. Demand forecasting requires a careful balance, drawing on historical sales data, market trends, and current consumer behavior. Businesses that neglect this analysis risk missing out on revenue or incurring unnecessary expenses.
2.- Lack of adequate inventory management
Poor inventory management is another key issue that often plagues businesses during the holiday season. When inventory is not tracked in real-time, it becomes challenging to know what’s available, leading to delays in order fulfillment or overselling products that are out of stock.
Manual processes or outdated systems exacerbate this problem. Implementing a robust inventory management system can help businesses monitor stock levels, automate restocking, and ensure that popular items are always available.
3.- Insufficient staffing and resources
Many businesses underestimate the need for additional staffing and resources during the holidays. With increased order volumes, longer working hours, and tighter deadlines, a lack of manpower can create bottlenecks in the supply chain.
Warehouses may struggle to pick, pack, and ship orders promptly, while customer service teams can become overwhelmed with inquiries and complaints. To avoid this, businesses should hire seasonal workers, train existing staff to handle peak demand, and ensure that resources like packaging materials and transportation are sufficiently stocked.
4.- Delayed or inefficient delivery planning
Delivery is a make-or-break factor during the holiday season, with customers expecting fast and reliable shipping. However, many businesses fail to optimize their delivery processes, resulting in delayed shipments or missed deadlines. Challenges such as poor route planning, insufficient communication with carriers, and last-mile delivery inefficiencies can severely impact customer satisfaction.
To address these issues, businesses should invest in delivery management tools, collaborate closely with shipping partners, and provide customers with accurate tracking information and delivery updates.
5.- Overlooking communication with suppliers
Strong supplier relationships are the backbone of a smooth supply chain, yet many businesses neglect to maintain clear and consistent communication with their vendors. Misaligned timelines, unexpected delays, or a lack of coordination can disrupt the flow of goods, leading to late shipments or incomplete orders.
To prevent this, businesses should establish open communication channels, share demand forecasts with suppliers in advance, and build contingency plans for potential disruptions. Regular updates and collaborative planning can go a long way in avoiding these issues.
6.- Neglecting contingency planning
As we mentioned above, the holiday season is unpredictable. Unfortunately, many businesses fail to prepare for these scenarios, leaving them scrambling to resolve issues as they arise. That’s why there are strategies like contingency plans, and the lack of having one can result in delays, dissatisfied customers, and financial losses.
To mitigate these risks, businesses should develop backup plans, such as alternative suppliers, emergency staffing strategies, and communication protocols for handling crises. Being prepared for the unexpected ensures resilience in the face of holiday season challenges.
Now that you’ve learned more about how to be prepared for the holiday season, share this article on social media, and stay tuned to our blog for more information and updates on the 2025 scenario for businesses and the logistics world.