Methods and tools to improve your order picking accuracy
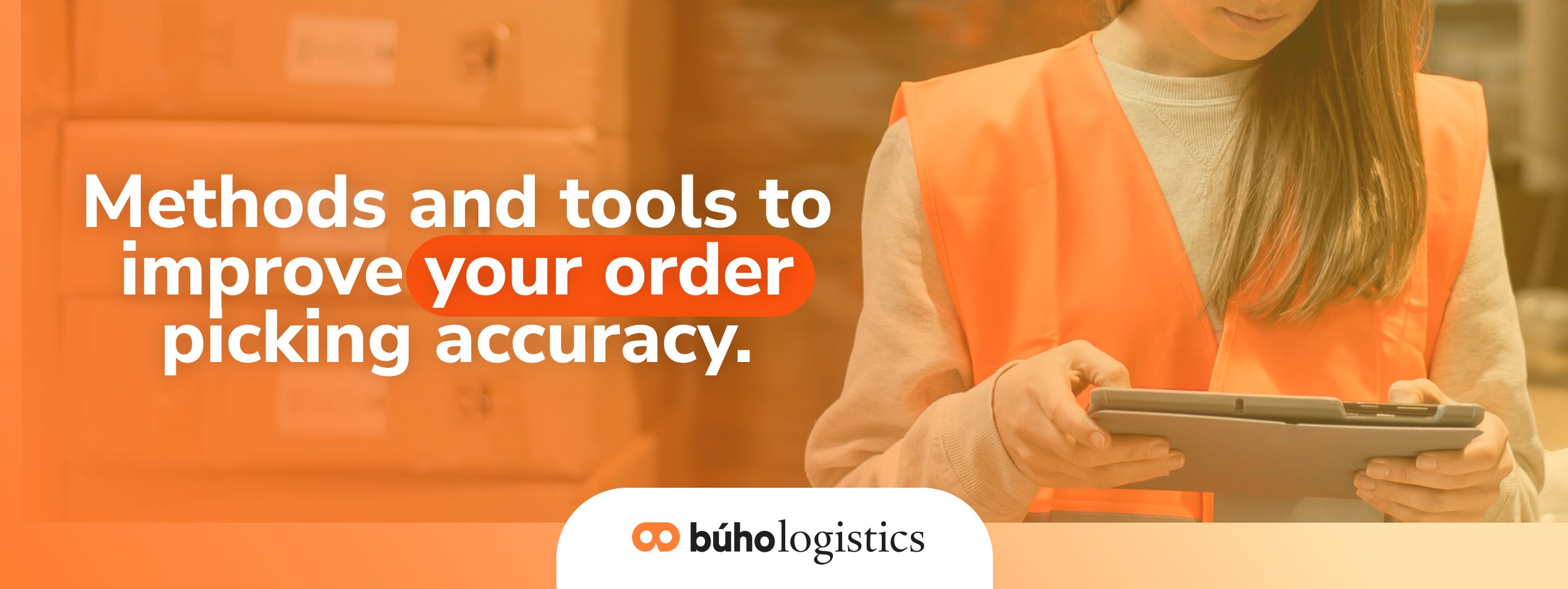
Contenidos
Order picking is critical in any warehouse or fulfillment center in Mexico, directly impacting customer satisfaction, operational efficiency, and profitability. Accurate order picking ensures customers receive the correct items on time, reducing costly errors like returns, reshipping, and damaged reputation.
However, achieving high accuracy in order picking can be challenging due to human error, inefficient processes, and complex inventory systems. In today’s environment, businesses must implement reliable methods and tools to improve order picking accuracy while maintaining speed and productivity.
In this article, we’ll explore some proven strategies and technologies that can help businesses enhance their order picking accuracy, reduce errors, and streamline warehouse operations. Whether running a small-scale operation or managing a large logistics center, these methods will empower you to deliver better results and boost overall performance.
Common challenges in order picking accuracy
Order picking is one of a fulfillment center's most labor-intensive and error-prone processes since it directly impacts quality control. Despite technological advancements and warehouse management practices, several challenges affect order picking accuracy.
These challenges stem from human factors, inventory complexities, and inefficient operational methods. Addressing these obstacles is critical for businesses looking to streamline operations, improve accuracy, and meet customer expectations. Hereunder, we explain these challenges a bit further.
1.- Human Errors
Human error is one of the most significant contributors to inaccurate order picking. Fatigue, distractions, and repetitive tasks can easily lead to mistakes such as picking the wrong item, incorrect quantities, or missing items altogether.
Workers in high-pressure environments, especially during peak seasons, may experience physical and mental exhaustion, further reducing their accuracy. Without adequate breaks, training, or support, these errors can accumulate and impact both customer satisfaction and operational costs.
2.- Complex inventory management
Managing inventory in large or disorganized warehouses poses a major challenge to order picking accuracy. Poor inventory visibility, inconsistent labeling, and misplaced stock can confuse pickers, leading to delays and errors.
In environments where inventory is frequently moved or replenished, pickers may rely on outdated information, resulting in picking from the wrong location or grabbing obsolete products. A lack of real-time inventory tracking compounds the problem, making it difficult to maintain accuracy in fast-moving warehouses.
3.- Inefficient picking methods
As we mentioned above, picking methods can greatly influence accuracy. Relying on outdated, manual picking processes —such as paper-based pick lists— can result in errors due to misread or illegible information.
Similarly, warehouses that use unoptimized picking strategies, such as single-order picking for high-volume operations, may struggle with productivity and accuracy.
4.- Lack of technology integration
Many warehouses still operate without adequate technology to support accurate order picking. The absence of tools such as barcode scanners, RFID systems, or Warehouse Management Systems (WMS) leaves pickers reliant on manual processes prone to human error.
Without technology to validate picks, identify stock locations, and provide real-time updates, achieving consistent accuracy becomes a significant challenge.
Methods to improve order picking accuracy
To address these challenges, you require a strategic approach that combines process improvements, workforce support, and the right technological tools.
By focusing on key methods, businesses can significantly reduce errors and improve the overall efficiency of their picking operations. Each of the methods we will develop hereunder, addresses specific challenges, making them essential for achieving high levels of accuracy.
1.- Optimize warehouse layout
The layout of a warehouse plays a crucial role in order picking accuracy. A poorly designed warehouse increases the chances of errors by forcing pickers to travel unnecessarily long distances or work in cluttered, disorganized spaces.
By reorganizing the layout to minimize travel time and streamline access to frequently picked items, businesses can reduce the physical and cognitive strain on workers.
2.- Implement order picking best practices
Standardizing workflows and implementing best practices can significantly impact order picking accuracy. Choosing the right picking method is an important first step. For example, single-order picking is ideal for low-volume operations, while batch or wave picking is more efficient in high-volume environments.
Additionally, clearly labeling storage locations and creating visual cues can help workers quickly identify the correct items. Quality control measures, such as double-checking picks before packing, can also catch errors early in the process. Developing detailed standard operating procedures (SOPs) ensures that all workers follow the same methods, reducing variability and the likelihood of mistakes.
3.- Invest in training and skill development
Even with advanced processes and optimized layouts, the human element remains a critical factor in order picking accuracy. Investing in comprehensive training programs ensures that employees understand their responsibilities, are familiar with warehouse layouts, and can efficiently operate any tools or technologies provided.
Training should include hands-on practice with barcode scanners, Warehouse Management Systems (WMS), and any other tools used in the picking process.
In addition to initial training, businesses should offer ongoing skill development opportunities, such as refresher courses or cross-training to handle different picking methods or technologies.
By combining these methods companies can create an environment that supports high order picking accuracy. If you liked this article don’t forget to share it on social media and stay tuned to our blog for more information regarding fulfillment optimization for your business.