Types of picking
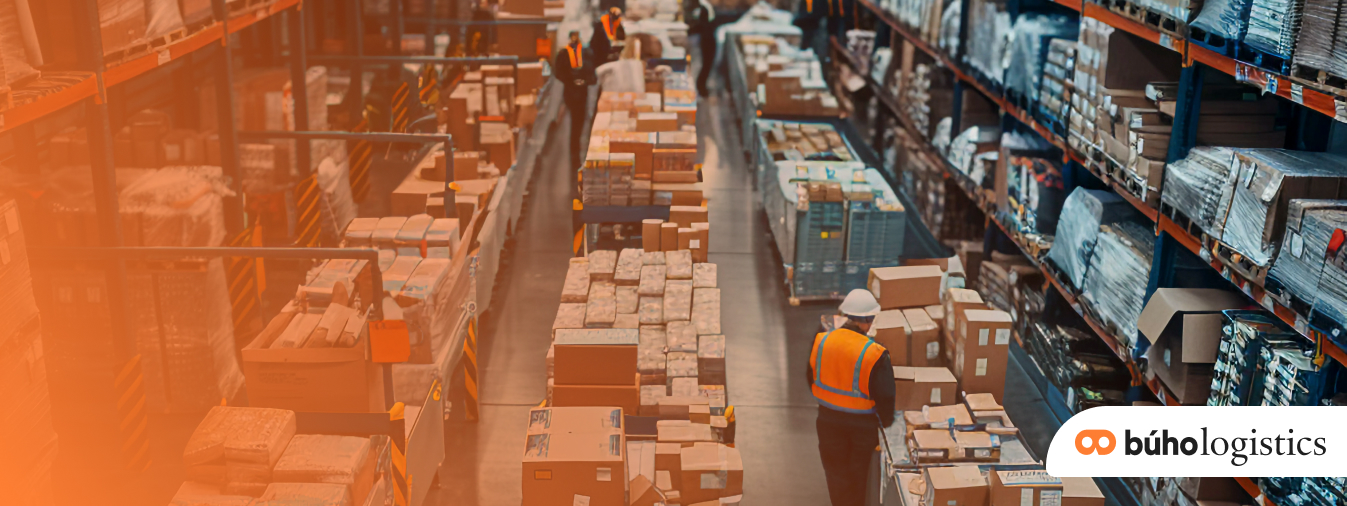
Contenidos
Last week, we discussed what RMA is and its importance in creating an efficient return process strategy. However, many returns could be avoided with the adequate picking technique.
Efficient order picking ensures smooth operations and timely deliveries in logistics and supply chain management. In a warehouse, fulfillment center, or retail store, picking refers to retrieving products from storage to fulfill customer orders.
There are several different picking methods, each tailored to specific operational needs, ranging from manual systems to automated solutions. This article explores the various types of picking techniques, their advantages, and how they contribute to optimizing workflow, reducing errors, and improving overall productivity in modern order fulfillment systems.
What is picking?
For those new to the fulfillment world, picking is the process of selecting and retrieving products from inventory or storage to fulfill customer orders. It is a crucial step in order fulfillment since it is where items are "picked" from their storage locations and prepared for packaging, shipping, or delivery.
Types of picking
1.- Manual picking or single order picking
Manual picking is one of the most common methods in warehouses and fulfillment centers, particularly for small to medium-sized operations. It involves workers physically retrieving products from storage locations based on a list of items needed for an order.
Once collected, the items are brought to a packing station or directly prepared for shipment. This method is versatile, as it can accommodate various product types and sizes, from small individual items to larger, bulkier goods.
One of the key advantages of manual picking is its flexibility. Since workers are handling the products themselves, they can easily adapt to changes in inventory, handle fragile or irregularly shaped items, and make real-time decisions when issues arise, such as stock discrepancies or damaged goods.
This flexibility makes manual picking suitable for operations with diverse products or frequent inventory changes. Additionally, manual picking has relatively low initial costs compared to automated systems, which require significant investments in machinery and technology.
2.- Batch picking
Batch picking is a widely-used order fulfillment strategy that focuses on improving efficiency by grouping multiple orders and picking items for several orders in a single trip through the warehouse.
Rather than picking items for one order at a time, batch picking allows workers to collect items for several orders simultaneously, reducing the number of trips required and minimizing travel time across the warehouse.
As you may see, one of the advantages is the significant reduction in picking time. By consolidating orders, workers can pick items more quickly, as they only need to visit a location once to collect all items needed for multiple orders. For example, if several orders contain the same item, the worker can pick all units of that item in a single trip rather than revisiting the same location multiple times.
This streamlined approach reduces walking time, improves productivity, and allows warehouses to process a larger number of orders in less time. In high-demand environments such as eCommerce or retail distribution, this efficiency is crucial to meeting customer expectations for fast delivery.
3.- Automated picking
A new trend within the logistics world is automated picking; it leverages advanced technology, such as robotics, conveyors, and automated storage and retrieval systems (AS/RS), to pick and move products with minimal human involvement.
By automating the picking process, businesses can handle high volumes of orders with precision, reducing the need for manual labor and optimizing workflow. Robots or automated systems can pick and move products faster than human workers, often working around the clock without fatigue.
This 24/7 operational capacity allows for quicker order fulfillment, meeting the growing demand for faster delivery times. Additionally, automated systems are less prone to errors, as they can be programmed to retrieve specific items precisely.
Another key benefit of automated picking is its scalability. As a business grows and order volumes increase, automated systems can easily scale to meet the demand. Automation is also ideal for handling repetitive tasks, freeing up human workers to focus on more complex or value-added activities, such as quality control, maintenance, or problem-solving.
4.- Zone picking
This type is a highly organized order fulfillment strategy in which a warehouse or distribution center is divided into different zones, and workers are assigned to specific zones to pick items for orders.
Each picker is responsible for retrieving products within their designated area and passing the order to the next zone if necessary. This method is particularly useful in larger warehouses where order fulfillment involves handling a vast inventory, and it is designed to minimize worker movement and increase efficiency by localizing tasks within manageable areas.
Now that you have learned more about some types of picking tell us which strategy suits your business best. Also, remember to contact us if you want to partner with a fulfillment center; one of our team members will be happy to assist you.