5 strategies to prevent warehouse inventory overstock
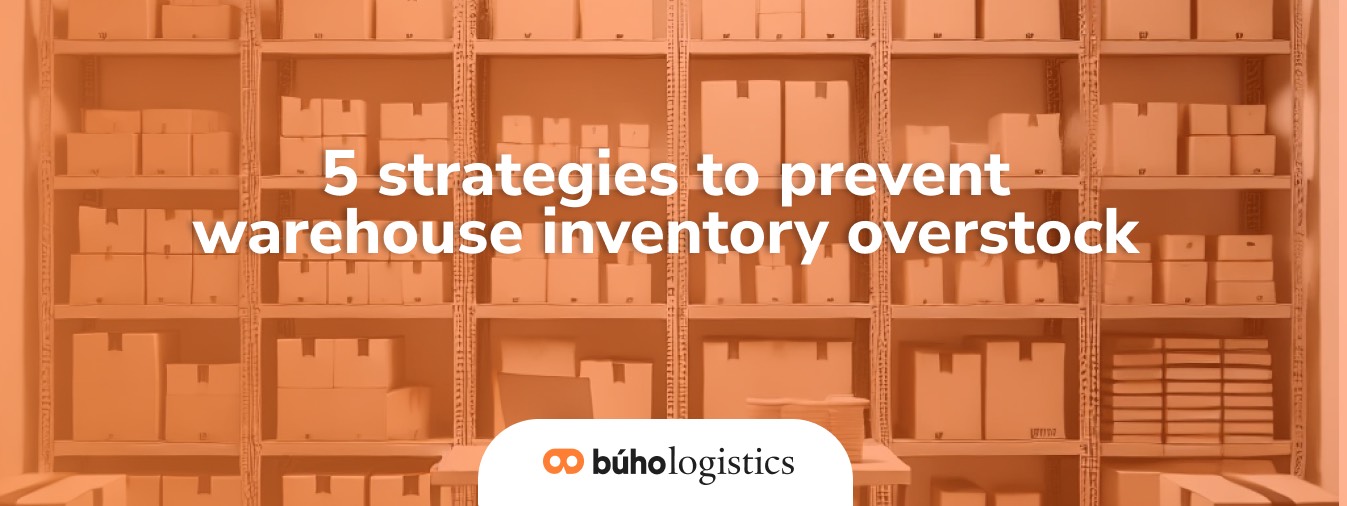
Contenidos
In our last article, we discussed how chatbots improve shipping and returning processes; here, you’ll find strategies that your business can use in order to enhance your transactions.
However, many elements must be improved to achieve success in the modern world. Effective inventory management is crucial for any business that relies on warehousing and distribution.
Balancing supply and demand requires a strategic approach to optimize inventory levels without tying up excess capital. In this article, we’ll explore five proven strategies to prevent warehouse inventory overstock.
1.- Implement data-driven demand forecasting
One of the most effective ways to prevent warehouse inventory overstock is by leveraging data-driven demand forecasting. This means that rather than relying on guesswork or outdated ordering habits, businesses can use historical sales data, market trends, and consumer behavior insights to predict the demand more accurately.
This also allows companies to identify seasonal fluctuations, peak sales periods, and slow-moving products, allowing them to adjust inventory levels accordingly.
Advanced technologies, such as AI and machine learning, have further enhanced demand forecasting accuracy. These tools can process vast amounts of data, identify emerging trends, and even predict shifts in customer demand before they happen.
As a fulfillment center in Mexico we know that by integrating AI-driven forecasting models, businesses can make more informed purchasing decisions, reduce excess inventory, and avoid costly overstock situations.
Additionally, external factors like economic conditions, competitor activity, and supply chain disruptions should be considered when forecasting demand. Regularly updating forecasts based on real-time data ensures that inventory levels remain optimized, reducing waste and improving overall operational efficiency.
2.- Optimize your supply chain processes
A well-optimized supply chain is essential for preventing warehouse inventory overstock. Inefficiencies in procurement, production, or logistics can lead to excessive stock accumulation, tying up capital and increasing storage costs. Businesses must streamline their supply chain by improving communication with suppliers to avoid this, enhancing coordination between departments, and implementing flexible restocking strategies.
One proven method to optimize inventory flow is Just-in-Time (JIT) inventory management. This approach ensures that stock arrives exactly when needed, reducing the risk of over-purchasing and excess storage. However, for JIT to be effective, companies must have reliable suppliers and a robust logistics network to prevent stockouts and delays.
Another key aspect of supply chain optimization is reducing lead time inefficiencies. Long and unpredictable lead times can result in businesses over-ordering as a precaution, leading to overstock. By analyzing supplier performance and identifying bottlenecks, companies can take proactive strategies such as diversifying their supplier base, investing in faster transportation options or leveraging digital supply chain management tools.
3.- Utilize inventory management software
Investing in inventory management software is a game-changer for businesses. Modern inventory management systems provide real-time visibility into stock levels, helping businesses make data-driven decisions about replenishment, order quantities, and product movement.
A robust inventory management system offers automation features that streamline stock control. Businesses can set up automatic reorder points, ensuring that new stock is only ordered when inventory reaches a predetermined threshold. Additionally, features like barcode scanning, RFID tracking, and cloud-based access enable warehouse teams to monitor inventory levels accurately and update records instantly.
Integration with other business tools, such as enterprise resource planning (ERP) systems and point-of-sale (POS) software, further enhances inventory control. They synchronize inventory data with sales, procurement, and supply chain operations to achieve a more holistic view of their stock flow.
4.- Set up stock replenishment strategies
Without a clear replenishment system in place, businesses may order excess stock out of caution, leading to high storage costs, wasted resources, and potential product obsolescence. To avoid this, companies must establish efficient replenishment methods that align with actual demand and consumption patterns.
One effective approach is setting minimum and maximum stock levels for each product, as we mentioned above. Regularly reviewing and adjusting these levels based on sales data, seasonal trends, and supply chain conditions helps maintain a balanced inventory.
Another essential replenishment strategy is using the Reorder Point (ROP) and Economic Order Quantity (EOQ) models. The ROP method triggers new stock orders when inventory reaches a predetermined level, ensuring timely replenishment without unnecessary surplus. While the EOQ model, on the other hand, calculates the ideal order quantity that minimizes both holding and ordering costs.
Regular stock audits and real-time tracking also play a crucial role in replenishment planning. By analyzing which products are moving quickly and which are slow-moving, businesses can adjust their replenishment schedules accordingly. This proactive approach not only prevents overstock but also enhances overall warehouse efficiency, improving cash flow and reducing waste.
5.- Improve warehouse organization and space utilization
Poor storage layouts, lack of categorization, and inefficient use of space can lead to misplaced inventory, over-purchasing, and difficulty in tracking stock levels. By optimizing warehouse organization and maximizing space utilization, businesses can improve inventory accuracy, reduce excess stock, and streamline order fulfillment processes.
One effective strategy is implementing efficient shelving and storage solutions. Vertical racking systems, modular shelving, and automated storage solutions can help maximize space and reduce clutter. You can categorize products based on demand frequency, such as keeping fast-moving items in easily accessible locations and slow-moving items in less prominent areas; businesses can improve inventory flow and reduce unnecessary stockpiling.
Adopting the First-In, First-Out (FIFO) method is another approach to inventory management. FIFO ensures that older stock is sold or used before newer stock, preventing product obsolescence and waste, particularly for perishable goods or time-sensitive products. This method also helps businesses identify slow-moving inventory, allowing them to adjust purchasing decisions to prevent overstocking.
We will always recommend performing regular stock audits and cycle counting to enhance warehouse efficiency further. Conducting routine inventory checks helps identify discrepancies between recorded and actual stock levels, preventing over-ordering due to inaccurate data.
Additionally, warehouse management software (WMS) can automate stock tracking, improve inventory visibility, and optimize storage allocation, ensuring that every inch of warehouse space is utilized effectively.
By focusing on these strategies, you can be sure that overstocking will never be a problem; on the other hand, you will create a more efficient supply chain. If you find this article useful, remember to share it on social media and stay tuned to our blog for more information regarding fulfillment optimization.