Importance of quality control in Third-Party Logistics
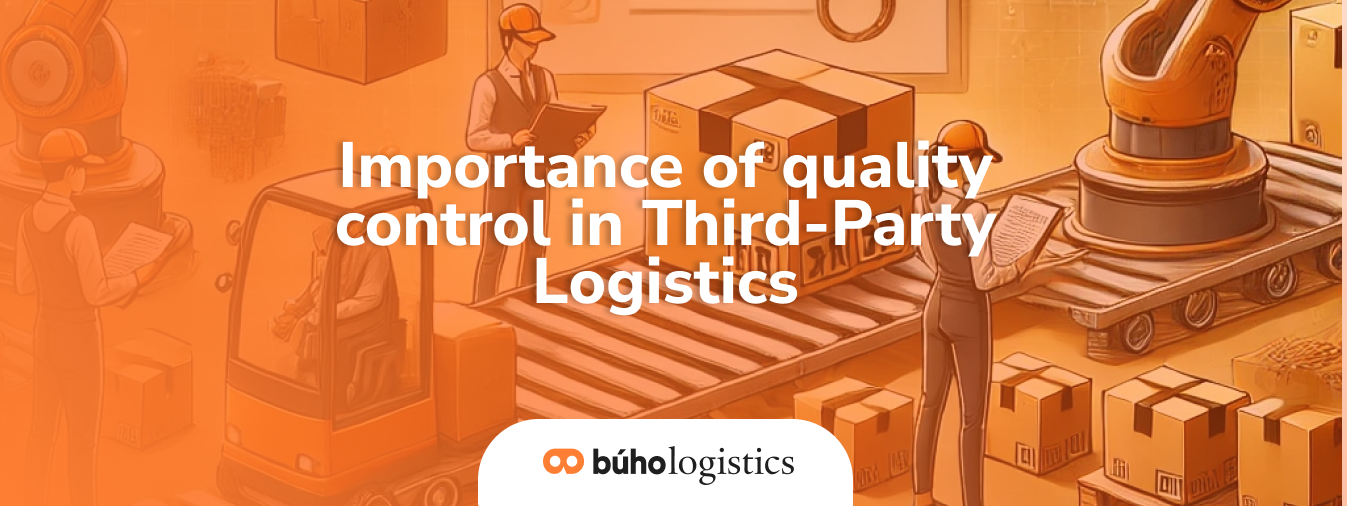
Contenidos
Do you already have your marketing strategies for this Black Friday? Well, what are you waiting for? In case you are struggling to meet the demand, we have great news for you: third-party logistics (3PL) providers play a crucial role in helping businesses streamline their supply chains.
Nowadays, most companies are outsourcing their transportation, warehousing, and distribution needs to the reliability and efficiency of 3PL partners. However, this reliance also raises a significant challenge: ensuring consistent quality in the services provided.
Quality control in 3PL is not just about meeting service level agreements; it’s about safeguarding a company’s reputation, ensuring customer satisfaction, and maintaining operational efficiency.
As you know, we are a fulfillment center in Mexico with the experience and expertise to share with you the importance of quality control in 3PL operations, highlighting its impact on supply chain performance. So, in case you are looking for a 3PL partner, we recommend you keep reading.
What is 3PL?
Third-party logistics (3PL) refers to outsourcing logistics and supply chain operations to external service providers. These companies handle various logistics functions, including transportation, warehousing, inventory management, and order fulfillment, enabling businesses to focus on their core competencies.
By delegating these critical operations, companies can streamline their supply chains and adapt more flexibly to market demands. 3PL providers bring specialized expertise, infrastructure, and technology to handle these processes. They cater to diverse industries, from retail and manufacturing to e-commerce and healthcare, offering tailored solutions to meet specific logistical challenges.
Key areas for quality control in 3PL services
As you may infer, effective quality control in third-party logistics requires focusing on specific operational areas to ensure seamless service delivery and client satisfaction. Below, we explore the key areas where quality control is critical, highlighting how meticulous management in these domains can drive success.
1.- Warehousing and inventory management
Warehousing is the backbone of any logistics operation, and maintaining accurate inventory records is paramount. Quality control in this area involves regular audits, efficient organization of products, and the implementation of advanced inventory management systems. Errors in stock levels or misplacement of products can lead to delays and customer dissatisfaction.
Additionally, warehouses must adhere to safety and hygiene standards, especially when handling sensitive merchandise. Implementing barcode scanning, RFID technology, and automated systems helps reduce human error and ensures that inventory is accurately tracked and readily available for dispatch.
2.- Transportation and delivery
Transportation is often the most visible aspect of 3PL operations, directly impacting customer satisfaction. Quality control measures in transportation focus on timely deliveries, minimizing damage during transit and optimizing routes for efficiency.
Also, your 3PL partner needs to ensure that vehicles are well-maintained and drivers are adequately trained, which is essential for reducing delays and avoiding costly incidents.
Some companies have monitoring tools like GPS tracking and fleet management software that provide real-time updates, enabling proactive resolution of issues such as traffic congestion or weather disruptions. By prioritizing quality in transportation, 3PL providers can consistently meet delivery deadlines and enhance client trust.
3.- Packaging and handling
Proper packaging and handling of the products is crucial to maintaining the integrity of goods throughout the supply chain. Quality control in this area involves selecting the appropriate packaging materials and ensuring products are packed securely to withstand the rigors of transportation.
Inadequate packaging can lead to damaged goods, resulting in dissatisfied customers and financial losses. That’s why we recommend that you make sure that the staff of your 3PL is properly trained in packing techniques or that they have automated packaging solutions to enhance efficiency and reduce errors.
4.- Real-time tracking and communication
Transparency and communication are critical for a seamless 3PL operation. Quality control in this domain ensures that clients and end customers have access to accurate, real-time updates about their shipments. Advanced tracking systems and integrated software platforms enable 3PL providers to monitor shipments closely and share updates proactively.
Clear communication channels also help address issues promptly, such as shipment delays or routing changes. By investing in technology and fostering open communication, 3PL providers can strengthen client relationships and create a more reliable supply chain.
The future of QA in 3PL
Lastly, what will the future hold for quality assurance in third-party logistics? The technological advancements we're living in permeate this part of the logistics world.
Automation and artificial intelligence are set to play an important role in streamlining QA processes. AI-powered analytics can predict potential disruptions, optimize routing, and monitor quality metrics in real-time, enabling 3PL providers to address issues proactively.
Additionally, adopting blockchain technology promises greater transparency by providing an immutable record of transactions and shipment data, which helps enhance trust and accountability. These innovations, coupled with IoT devices for real-time monitoring of products, will allow 3PL providers to maintain higher quality standards and adapt swiftly to changes in supply chain dynamics.
Now that you've learned more about quality control in 3PL, remember to contact us, our team is always ready to help you and your company on your road to success. Also, if you find this article useful, share it on social media and stay tuned to our blog for more information.